A question on shielding with plain aluminium
02 Feb 2023
Question:
Do you think it would be reasonable to create an RF/EMI shield out of plain aluminium, where the flanged box lid (yellow in the image below) and its baseplate (blue) are connected through large mating surface areas that are thoroughly cleaned beforehand to remove any oxidation layers and then firmly bolted together (the many small red items in the image above)?
I.e., would it be difficult to create a good RF-bond at all the (red) joints?
If not, is it possible to alochrome or iridite only the mating surfaces, to reduce cost? Or can this process only be applied to the full metal object?
Answer:
The problem is that “…firmly bolting together…” will not create gas-tight metal-to-metal joints!
Except for method a) below.
Air will get in, so eventually all the aluminium contact surfaces will get converted to aluminium oxide – a tough non-conductive ceramic.
I.e., the metal contacts needed to achieve the shielding will not be made of metal any more, but tough ceramic insulators. Shielding effectiveness will therefore eventually be lost.
But there is worse!
The RF resonant cavity (or cavities) inside what was supposed to be a shielding box will amplify certain frequencies, which could make the EMC worse than it would have been without the box at all! This can usually be mitigated by placing a sufficient amount of a suitable RF absorber, in a suitable location inside the box, increasing both the BOM cost and the cost of assembly.
The solution to using plain aluminium, is to ensure all the shielding joints are reliably ‘gas-tight’.
This can be done by:
1) Cleaning the aluminium contact areas of oxide (as much as possible, anyway, there’s always some that forms immediately) and all contaminants, including moisture, before assembly, then not touching the surfaces at all;
2) Not relying on the fixing parts themselves (screws, rivets, etc.) for the contacts that help create the shield;
3) Making the joints between aluminium contact areas impervious to penetration by gasses and/or vapours and/or liquids;for example, by:
- Cold-welding with massive pressure, making the box almost impossible to remove and impossible to replace;
- ‘Hot welding’ (e.g. arc, gas, spot, laser, etc.), making the box almost impossible to remove and impossible to replace;
- Using conductive gasket types that are also environmental seals which ensure reliable gas-tight joints over the operational life and do not cause any kind of corrosion (galvanic, fretting, etc.) in contact with the plain aluminium joint surfaces, examples of these include:
- Certain types of solid elastomers, which need reliable mechanical pressure – depending on the type – to compress correctly, so need reliable fixings;
- Caulks, which make the box easy (but messy) to remove/replace, but have no adhesion or strength so need reliable fixings;
- Liquid ‘form in place’ elastomers, which make the box difficult and messy to remove/replace, but provide some adhesion and strength (with suitable surface preparation) – depending on the type – so might be able to be used without fixings;
- Liquid ‘form in place’ epoxies, which make the box very difficult indeed, and messy, to remove/replace, and are strong in adhesion (with suitable surface preparation) – depending on the type – so can often be used without fixings.
Alternatively, convert the surfaces of all aluminium contact areas into a conductive material that oxidises at a much lower rate, before assembly.
For example, by:
4) Alochroming, using legal trivalent chromium (Cr3) processes developed since hex-chrome (Cr6) processes were (rightly) banned;
5) Iriditing, I understand this chromium-free process is offered by almost all metal platers;
6) Tin plating – the second best!
This is a two-step process, see https://www.finishing.com/40/39.shtml.
However, with suitable masking it may not be as costly as expected);
7) Gold plating – the very best! Does not oxidise at all.
This is at least a two-stage process, see https://www.finishing.com/192/74.shtml.
However, with suitable masking it may not be as costly as expected.
8) Copper tape with a pressure-sensitive conductive adhesive,
but requires diligent preparation of both joint surfaces as described above, followed immediately by applying the tape in the appropriate manner whilst taking great care not to touch the bare joint surface or the adhesive where it will contact the joint surface.
However:
It needs skilled manual assembly.
May not be totally gas-tight initially, and will eventually start to leak over time depending on the type of adhesive, method of assembly, and the physical and climatic environments;
9) Coating with a conductive (usually nickel-zinc) polymer,
not recommended – because it is costly, and difficult to maintain quality in manufacture.
It is perfectly possible to expose only the contact areas to conversion/plating, by ‘masking-off’ the surfaces that are not to be converted/plated. Platers should be very experienced and skilled at masking-off, but each will do it differently so ask their advice.
Unfortunately, I quite often see shielding that has been fatally compromised by poor quality masking-off, where paint (or whatever) covers part of the area required for RF-bonding. So, I recommend checking some examples before choosing your plater. Of course, they will show you good examples, so try to get to see (and check) their normal production quality in their plant.
Even so, I recommend appropriate inspection before accepting any batches from platers/painters into manufacturing stores. Inspection should cover surface conductivity (using very smooth low-pressure resistance probes) and a visual check that the masked-off areas do not intrude at all into any parts of the shielding joint areas. Remember, the only way to ensure 100% quality control, is to inspect/test every single characteristic that is specified! So, except for one-off custom products, there is always a compromise to be made on quality of manufacture.
All the details of all the above are covered by my two-hour training course: “Module 4”, on shielding from DC to over 60GHz.
For a colour-PDF of its coursenotes, see https://www.emcstandards.co.uk/shielding-for-emc.
A video webinar of it will be made available in 2023, from https://emcstandards-shop.fedevel.education/index.html.
If you want the answer to this and many other EMC/EMI questions please join me for training in May - click here for more information!
Get more from EMC Standards
EMC Standards is a world-leading resource for all things EMC and EMI related. Our website is packed full of both free and paid-for content, including:
- Online quiz
- Webinars
- Training quiz
- And much more!
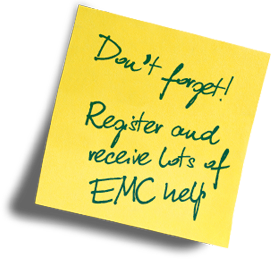
Electromagnetic Engineering (EMgineering) is the basis for proven good design practices for signal integrity (SI), power integrity (PI), and the control of EMI emissions and immunity (EMC).
Our aim is to help people learn how to more quickly and cost-effectively design and manufacture electronic equipment (products, systems, installations, etc.) to meet functional (i.e. SI/PI) specifications and conform to EMC standards, directives and other requirements.
Such equipment should benefit from reduced warranty costs and financial risks, whilst improving uptime, competitiveness and profitability.
We also cover basic good electrical safety engineering; and the Risk Management of Electromagnetic Disturbances / EMI, whether for Functional Safety or other types of risk.
Join EMC standards TODAY!